Content
It also helps a company in minimizing the total investment in inventory. Below the entry for WIP inventory, you can record the raw materials inventory. The raw materials inventory consists of all the parts the company hasn’t used yet for manufacturing purposes.
- Finished goods refer to the final stage of inventory, in which the product has reached a level of completion where the subsequent stage is the sale to a customer.
- Before you record your entry, it’s important to review the calculations for accuracy to make sure you included all the relevant costs.
- When work in progress limits are working for the team, an issue’s cycle time will drop.
- Some business owners assume that WIP can stand for “work-in-progress” or “work-in-process” and that these terms are interchangeable.
- This can be a bit time-consuming, so it’s typically best to tally it up at the end of your accounting period to minimize uncertainty on your company’s balance sheet.
- These dates are used in a few different areas of the report from determining if a job will appear to what costs are pulled in.
- Below is a sample agile board with WIP limits used by a typical software development team.
Another example of when a company might use job costing is if they create high-end, custom products. If a company is building custom furniture, they know the specific costs that went into each piece of furniture. Investors and analysts can also use work-in-progress when they are looking at a company’s production process. Imagine that a company has more products in work-in-progress than it usually does, but its sales haven’t increased. This increase might be a sign that there are bottlenecks in the production process, and things aren’t running smoothly — or that the business has reason to believe sales are going to spike soon. Once a company has used the materials in the production of a good, those materials are moved on the balance sheet to the work-in-progress category.
Calculate The Manufacturing Costs
Removing these bottlenecks will reduce the WIP time, maximizing output. These bottlenecks can be removed by allocating more resources to that stage, usually employees or materials. Maintaining a high level of work in progress shows inefficiency in the entire production process. In addition, a high WIP indicates that a significant amount of capital is tied up within the business, leading to constrained cash flow and fewer profits. This content is for information purposes only and should not be considered legal, accounting, or tax advice, or a substitute for obtaining such advice specific to your business. No assurance is given that the information is comprehensive in its coverage or that it is suitable in dealing with a customer’s particular situation.
Your name, phone number, and e-mail address are subject to the submission of personal data. Fields such as time and disbursements are presented as links so you can drill into the details. If you attempt to add or drag a task to a status that has reached it’s limit, you’ll see a notice. When WIP inventories get transferred from one process to another, they still remain work-in-progress. The closing carried over value from one process becomes the opening value for the next. A point to note is that not many lenders would give a loan with the WIP as collateral since it will be difficult to sell WIP units in case a borrower defaults. Nevertheless, all external parties such as bankers, bonding agents, lenders, and underwriters evaluate work in progress to know the creditworthiness of the firm.
Work In Progress Accounting Management
The goal here is to optimize the team over the medium-term, and the short-term awkwardness is actually a good thing. After the team uses their WIP limits for a few weeks, make adjustments as needed. Resist the temptation to raise a WIP limit just because the team keeps hitting it.
To calculate WIP inventory, you need the beginning work in process inventory, and to calculate that, you need the ending work in process inventory. Too much WIP inventory increases the risk of materials becoming lost, broken, expired, or obsolete before they have a chance to be assembled. All of the following terms are under the umbrellas of manufacturing inventory. Data and analytics, and expertise you need to help you make better business decisions and keep customers happy. They have legally earned $4,000, given that they have completed 40% of the work; they just have not invoiced it yet.
Why Do I Have To Complete A Captcha?
So, when the run their profitability reports, they should see $4,000 in earned revenue for that line item. Is the amount an asset increases in price from when you buy it to when you sell it. New customers need to sign up, get approved, and link their bank account.
This makes up expenditure and as expenses come as invoices it is sometimes referred to as such. Some inventory management solutions allow you to set WIP limits so you can ensure you never have too many units at once.
Benefits Of Automating Wip Management
The Work In Progress refers to the work that can be in one out of many different stages of the production system, between the raw material and the finished product. Throughout the course of typical operations, manufacturers https://www.bookstime.com/ will generally have products in various stages of completion. This is especially true for manufacturers of large, complex, and time-consuming products such as machinery and other industrial equipment.
I think of work-in-process as the goods that are on the factory floor of a manufacturer. The amount of Work-in-Process Inventory would be reported along with Raw Materials Inventory and Finished Goods Inventory on the manufacturer’s balance sheet as a current asset. Some companies do a physical count of their WIP inventory to determine the value based on the current stage of each unit in the manufacturing process. This eats up huge amounts of valuable time and distracts your team from doing higher-level work. The contractor has not billed for the line item yet, but has already spent $2,000 in labor costs on the item, and is on schedule (about 40% complete).
Goals For Agile Teams Using Wip Limits
The beginning WIP inventory cost refers to the previous accounting period’s asset section of the balance sheet. To calculate the beginning WIP inventory, determine the ending WIPs inventory from the previous period and carry it over as the beginning figure for the new financial period. Any raw material inventory that humans have worked on but is not yet considered a finished good is a work-in-process inventory. You can think of WIP inventory as all inventory that has not yet reached the finished product inventory but is not raw materials. If you find your WIP units often exceed the limits you set, you’ll need to figure out how to reduce these manufacturing costs fast.
It can also be used for an asset where the value is expected to increase after the work is finished. During the work money spent towards completing a product or a service can be seen as a company asset. However, because of the reason that the work has not yet been completed, the monetary values incurred from WIP should be kept in separate accounts during the in-progress period. Since WIP inventory is an inventory asset, neglecting to include it on your business’ balance sheet can cause your total inventory to be undervalued. For tax purposes, it’s best to track WIP inventory to get an accurate breakdown of what your inventory is actually worth.
Agile has had a huge impact on me both professionally and personally as I’ve learned the best experiences are agile, both in code and in life. You’ll often find me at the intersection of technology, photography, and work in process motorcycling. Note that in the agile board above, the team has too many code reviews, so the column has turned red to indicate that. I’m a native New Yorker and I love everything connected to IT service management .
Work In Progress is an accounting concept meaning the value of the work you have completed but have not yet invoiced. WIP reports can also help you manage your cash flow, since they give you a sense of what your billings are likely to be at the end of the month.
WIP is also used in the construction industry, where companies calculate the proper billing time when the contract calls for percentage completion billing. So, a construction company will bill its client at various stages of the project. For instance, Construction Company X may send an invoice when it hits 25% completion, 50% completion, 75% completion, and, finally, at 100% completion. A piece of inventory is classified as a WIP whenever it has been mixed with human labor but has not reached final goods status. WIP, along with other inventory accounts, can be determined by various accounting methods across different companies. It’s particularly important to monitor supply chain efficiency in a time of unprecedented supply chain disruptions leading to raw material shortages and extended lead times. These elevated lead times have led many merchants to forecasting demand and procuring inventory 6 months in advance .
Is when a company hires other companies or individuals to perform services and labor outside of its organization instead of hiring employees. The articles and research support materials available on this site are educational and are not intended to be investment or tax advice. All such information is provided solely for convenience purposes only and all users thereof should be guided accordingly. Total WIP Costs are calculated as a sum of WIP Inventory + Direct Labor Costs + Overhead costs. The restaurant may also have capital costs like monthly rent payments for its premises and maintenance on equipment used to make food. The figures for both work in progress and work in process are listed on a company’s balance sheet. Andy Smith is a Certified Financial Planner (CFP®), licensed realtor and educator with over 35 years of diverse financial management experience.
Remember that the cost of the work-in-progress will vary depending on where a product is in the supply chain. When a company first purchases the raw materials they need to produce a good, those raw materials typically appear on the balance sheet as their own separate subcategory of inventory.
Published By
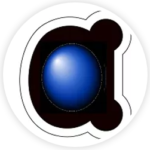